By Stacey Phillips, Autobody News
Published Feb. 7, 2023
In the 1930s, Lee Hunter Jr., a 23-year-old architectural student in St. Louis, MO, often had a dead car battery in his Packard convertible. He set out to create a device that would reduce battery charge time. In 1936, he introduced the Kwikurent, a battery charger that reduced charging time from 24 hours or more to less than an hour.
After serving in the U.S. Army Corps of Engineers and the Ordnance Corps during World War II, Hunter founded Hunter Engineering Company in 1946 and introduced the Tune-In wheel balancer.
As the company grew, Hunter developed other innovative equipment. Hunter’s team of engineers has received more than 350 patents and set many industry precedents, including a simplified lightbeam alignment system, a computerized dynamic wheel alignment and the thrust line principle, which many say is the foundation of modern four-wheel alignment.
For his impact on the automotive industry, Hunter was inducted into the Automotive Hall of Fame in 1992.
Today, the company is known for designing, manufacturing and selling a wide range of equipment, including computerized wheel balancers, tire changers, alignment racks, on- and off-car brake lathes, vehicle lifts, autonomous alignment and tire inspection equipment and ADAS calibration tools.
Tom Settle, director of field development and training, said Hunter’s award-winning patented alignment systems are used by independent shops, regional and national chains, dealerships and OEM manufacturing facilities worldwide.
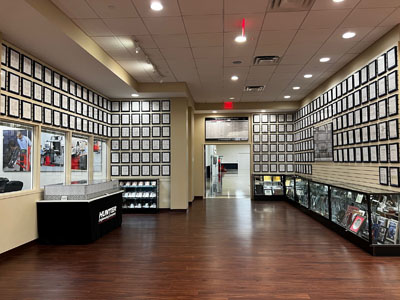
The equipment is manufactured in four plants---three in Mississippi and one in Bridgeton, MO, where a research and training center is located. Also in Bridgeton is Hunter’s 26-acre global headquarters. The company has international offices in Canada, Germany and China.
“Unlike most other manufacturers, all printed circuit design and assembly is performed in-house and produces over a million boards and cable assemblies every year,” said Settle. “This allows the company to create new products faster and maintain superior quality control.”
Throughout its history, the company has been focused on the automotive repair side of the business.
With the shift to electric vehicles (EVs), Steve Dawson, Hunter’s regional manager in the Washington, D.C. area, said the biggest growth over the next nine years will be in ADAS calibrations. As a result, the company has developed products to meet these needs, such as the ADASLink® diagnostics scan tool powered by Bosch. The equipment allows for dynamic (driving) ADAS calibrations as well as static (fixture) ADAS calibration with the Bosch DAS 3000. The DAS 3000 uses built-in cameras and rear wheel-mounted targets to position the fixture.
“We see tires, electrification and ADAS being critical [in the future],” said Dawson. “ADAS is expected to grow 400% from 2021 to 2030.”
With these changes, Dawson predicts automotive service will ultimately focus on the undercar.
“Shops that are not prepared for undercar in the EV world are going to be missing the boat,” he said. “Gone are the days of basic services, such as oil changes, that used to be the bread and butter of a repair shop.”
Hunter Products Showcased at SEMA
During the November SEMA Show in Las Vegas, NV, Hunter showcased its products and equipment.
Hunter’s latest innovation, unveiled during the show, is the Hunter Maverick™ tire changer, which uses some of the same technology as the Revolution™ fully automatic tire changer.
Settle said the machine allows technicians to control the tire-changing process using variable controls.
“What we find in the body shop world is that fully automatic balancers and tire changers make life easier, especially for those who don’t have the knowledge or ability,” he said.
Another tire changer on display was the Hunter Revolution™. Using the semi-autonomous WalkAway™ mode, Settle said, the machine does all the heavy lifting. “If I’m in a body shop environment and I'm not a seasoned tire technician, I can go out to this particular tire changer and all I have to know is the diameter of that wheel and tire and then let the machine do the work,” he said.
Settle also shared information about the Hunter Road Force Elite® wheel balancer. He said the balancer can perform a Road Force® test and balance faster than a traditional balancer and diagnoses vibration issues traditional balancers often can’t identify. It also automatically measures wheels dimensions with its patented vision system.
Hunter sales representative Will Cronin said proper alignment is extremely important, especially with ADAS on vehicles today. Visiting shops within his designated territory, Cronin finds repairers aren’t always familiar with how to do a calibration.
“Today, many body shops have generalists who do a little of everything,” said Cronin. “Hunter’s equipment is easy to use and cuts down time dramatically.”
The Hunter HawkEye Elite® is the company’s fully integrated alignment system, which can capture alignment measurements in 70 seconds. Using WinAlign® software, Settle said four precision cameras provide alignment measurements with a high degree of accuracy, providing fast and efficient readings. The equipment can be integrated with other shop systems, providing flexibility.
The equipment includes step-by-step guidance that walks technicians through the entire process. “If you are new to the industry as far as doing alignments, you can follow along, while also utilizing the onboard training information,” he said.
Sales representative Steve Booz said shops often ask how to incorporate the equipment into their business due to space limitations. “The equipment is designed with portability in mind, so it can be moved around the shop as needed.”
By partnering with Bosch, Booz said customers can be assured they have support from both companies.
Hunter exhibited the ADASLink® diagnostic scan tool as part of the SEMA ADAS Showcase.
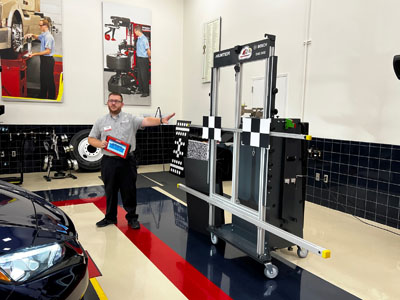
“With the interest ADAS is generating now and will be in the future, we’re eager to help inform and educate the industry about servicing these critical safety systems,” said Ryan Gerber, Hunter ADAS product specialist.
With ADASLink®, shops can connect the vehicle communication interface (VCI) to the vehicle’s OBD-II port to diagnose and interact with the car. A live camera-guided interface allows technicians to position the fixture properly and an on-screen walkthrough explains how to place the calibration targets. The equipment can calibrate forward-facing radar and camera sensors as well as side and rear sensors, including blind spot and surround view calibrations.
Technicians can also perform dynamic, driving calibrations with ADASLink® plugged into the vehicle.
The solution integrates with Hunter’s WinAlign® software, providing technicians with access to specific calibration procedures for more than 25 million vehicles.
Jesse Mincer, another Hunter sales representative, said a common concern from shops is not having a level floor. To address this challenge, Mincer said the portable system can change the level of the framing system where the targets are.
By doing calibrations in-house, he said it saves shops time and allows them to control the work. The work done on the vehicle is then documented, archived and saved in the cloud using HunterNet® 2. This online customer portal was developed for undercar service operators with single or multiple rooftops, featuring online service guides, equipment manuals, IoT capabilities and more.
“None of the technology is fruitful without having some training involved,” said Settle. More than 450 representatives across the country are tasked with installing Hunter equipment and conducting operational training.
In addition, Hunter offers a variety of educational opportunities for the industry focused on efficiency and profitability. These include online video tutorials on the YouTube Hunter Learning Channel, free self-driven e-learning classes through the Hunter University program, tuition-based onsite training at 47 centers across North America, as well as custom training at the corporate headquarters.
Since its inception, Settle said, Hunter Engineering has focused on creating efficiency and productivity for customers.
“One of our goals in 2023 is developing strategic solutions for collision repairers so shops can get vehicles repaired efficiently and be profitable at doing it,” he said.
Stacey Phillips Ronak