In the seven years since Kenny and Amanda Allen opened their Oklahoma City, OK, collision center, Allen Auto Body has become a go-to destination for customers seeking top-quality repair services. As a testament to their culture of excellence, the I-CAR Gold Class-certified shop offers a lifetime workmanship warranty, holds OEM certifications from Nissan, Infiniti, Hyundai, Kia, Chrysler, Jeep and Dodge, and has been named one of three best-rated body shops in the city.
Allen Auto Body
Oklahoma City, OK
405-948-1315
www.allenautobody.com
Facebook: @Allenautobodyokc
Instagram: @Allenautobodyokc
Company At A Glance...
Type: Collision Repair
Facility Employees: Five
In Business Since: 2016
Number of Locations: One
Production Space: 9,250 square feet
“Amanda and I have been in the industry more than 30 years,” said Kenny, whose career as a painter was inspired by a high school shop class. “She started as a parts delivery driver and then managed an independent shop. We met at the Ford dealership where I was the shop manager and she was the estimator. Later on, I was a paint rep for DuPont. She was a field appraiser for an insurance company. Then came the opportunity to buy this shop. With her skills and my background, we make a good team.”
Kenny oversees the shop. Amanda serves as estimator and back office administrator. They employ two I-CAR-certified body techs and a painter. Their daughter Hope doubles as receptionist/ customer service rep and handles parts intake. The 9,250-square-foot facility churns out 25 to 30 vehicles monthly. Most vehicles are less than seven years old.
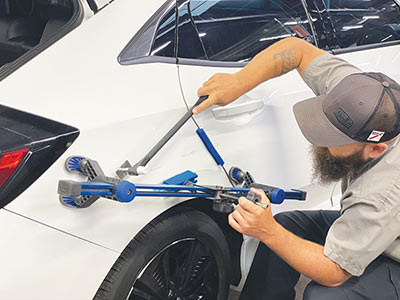
From the get-go, they opted to work directly with consumers rather than through a direct repair program. “Our initial approach was to be a DRP, but the guidelines didn’t meet what we wanted to do as a business,” said Kenny Allen. “We saw a greater need to work directly for the customer, not the insurance companies. It’s paid off; most of the time we get our door rate.”
Their approach to training, technology and tooling has paid off as well. “We’ve always wanted to be the best shop in town and invest as much as we can to stay up to date,” said Allen.
Through participation in the Assured Performance network, the shop secured its OEM certifications and earned the Assured Performance Certified designation. To assure compliance with OEM repair guidelines, including calibrations, the team relies on ALLDATA and RepairLogic’s OEM-specific software procedures.
To sharpen skills, techs participate in off-site training. Both owners also attend management-training classes. To stay abreast of legislative and regulatory issues, Amanda serves on the board of the Oklahoma Auto Body Association (OKABA.)
Staying up to date also means having the latest in tool technology. Like many automotive techs, Allen is enamored of tools and gadgets to improve efficiency, workflow and profitability, which is why he firmly believes the KECO Glue Pull Repair System is an asset to his shop.
When using the GPR System, Allen noted a significant difference from invasive old-school repair techniques. “Not having to grind a panel and sand body filler is a benefit. Employees aren’t breathing in as many hazardous materials. Because we don’t grind off the paint, the factory corrosion protection isn’t compromised and, with less dust and cleanup, there’s a faster turnaround.
“Before KECO GPR,” he added, “it seemed faster to beat the panel, grind it off and put on body filler. At first there was a learning curve with the KECO system. But now, it’s the first thing the techs turn to. Watching them use KECO GPR, I see new talents develop.
“With the paint still intact, they’re able to see whether the panel needs Glue Pull Repair or knock down. Once straightened, very little filler is needed. With GPR, they can work out the dent and make a less invasive repair. This has reduced our body filler and primer consumption, and the need to sometimes blend adjacent panels.”
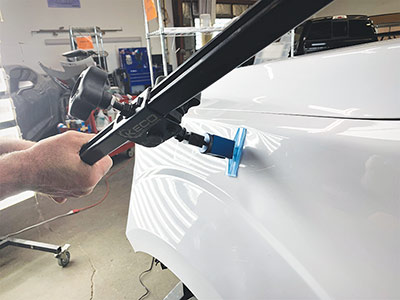
KECO GPR has also created an opportunity to repair minor damages to an EV. “Before GPR, if an EV showed up, we couldn’t repair it,” said Allen. Noting the GPR system complies with OEM guidelines, he said “it has opened a door for us. If it’s a cosmetic repair to the sheet metal, we can repair it with the KECO system.”
Training also plays an essential role. “At Allen Auto Body, training through KECO is a must,” said Allen, whose shop is close to KECO headquarters. “I was able to attend one of the very first training classes. I was amazed and excited to see all the possibilities the new systems were going to offer, and I’m still amazed at the possibilities. KECO is constantly coming out with new ways to help the industry.
“To stay up to date, you must invest in your equipment, training and new technology. If you’re not using KECO GPR, you’re going to fall behind. It’s a faster turnaround, it reduces material costs, it keeps your shop cleaner and you make more money. It's a win-win."
KECO Body Repair Products
405-745-2145
Company Contact: Scott Stayton
www.kecotabs.com
Facebook: @KECOBodyRepairProducts
Twitter: @kecotabs
Instagram: @kecodentrepair
LinkedIn: @keco-body-repair-products
YouTube: @KECOBodyRepairProducts
To read more auto body shop profiles in the October 2023 Shop and Product Showcase, click here.