Since the first collision repair facility joined Rivian’s Certified Collision Network (RCCN) in Oregon in July 2020, more than 30,000 Rivian electric adventure vehicles have been manufactured and 135 shops are part of the RCCN program.
Frank Phillips, senior manager, certified collision North America at Rivian, discussed the OEM’s certified collision network program during the AkzoNobel ACOAT Selected North American Performance Group (NAPG) event in Florida earlier this year.
Rivian was founded in 2009 as Mainstream Motors by Robert "RJ" Scaringe and later renamed Rivian, a wordplay on the Indian River in Florida, where Scaringe grew up. The company, headquartered in Irvine, CA, began focusing on autonomous and electric vehicles (EVs) to create products and services that help the planet transition to carbon-neutral energy and transportation.
Today, Rivians are built in the U.S. at the company’s approximate 4 million-square-foot manufacturing facility in Normal, IL, a former Mitsubishi factory.
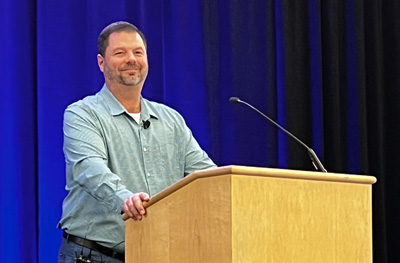
Currently, three products are being produced. The OEM’s flagship R1T, introduced in September 2021, was ranked “Best EV Ownership Experience among premium Battery Electric Vehicles” by J.D. Power in 2023.
The company also manufactures a seven-passenger SUV, the R1S, which received the Insurance Institute for Highway Safety (IIHS) TOP SAFETY PICK+ for the 2023 model year. In addition, Rivian has been contracted to develop and manufacture 100,000 electric delivery vans (EDVs) for Amazon.
Currently, Rivians can be purchased online. As part of owning one, the auto manufacturer offers insurance policies to customers in 48 states through Rivian Insurance Services, LLC. The agency provides auto, homeowners, renters, umbrella and more.
Phillips said the OEM has created a unique culture with a personalized customer experience.
“We have loyal customers who have stood in line for four years in some cases---when the Rivian was launched in 2018---to get their vehicle,” said Phillips. “We still have several others patiently waiting to get theirs. It's important to us to create an experience that returns that loyalty.”
Rivian has established a similar experience and culture with its certified network program.
“We believe it is really going to disrupt what many of the OEM programs around the country have done traditionally when it comes to certification,” said Phillips. “We want to make sure that shops are properly trained, educated and equipped to fix the Rivian safely and properly.”
He said Rivian's approach is to revolutionize the industry by creating an efficient and highly trained collision repair network.
“That's our focus every day,” he said. “When we wake up and come to work, we start thinking about how we are going to help our collision certified network become better and continue to improve.”
The certified network consists of four programs, one for its passenger vehicle line, another for the OEM’s commercial line, which allows facilities to repair Amazon EDVs, and a third for the business-to-business segment. In addition, a new program is being introduced this year for diagnostic certification focused on calibration.
In addition to Phillips’ counterpart in Amsterdam, Hank Berkhof, the team is led by Kelly Logan, senior manager of collision repair, and his engineering team, which includes Dan Black, manager of service engineering; David Sosa, manager of the R&D workshop; Brandon Chittenden, manager of service vehicle data; and Taylor Jozwiak, technical collision repair operations manager.
Phillips said they are all experienced technicians who have worked in body shops in different capacities. “They've all been boots on the ground in that difficult situation that you guys find yourselves in every day, and that's fixing the car that has been wrecked,” he said.
The team regularly visits its network shops to offer support and ensure their success. In addition, Rivian has a vendor program geared toward business-to-business relationships.
Rivian’s service engineering department uses CAD to determine how to repair cars safely and properly and then develops clear, effective and efficient repair and calibration procedures, ensuring compliance.
The procedures are then sent to the collision research and development workshop, where a hands-on validation of the repair procedures, tools and equipment is performed at the OEM’s collision center to ensure accuracy and quality.
“We do everything from paint to structural repairs,” explained Phillips. “It’s important that we make sure our paint color matches the availability of formulas.”
Collision centers that are part of Rivian’s certified repair network are then provided with the vehicles’ repair methods and procedures.
“Independent collision centers have made the commitment to partner with Rivian and we want to provide the tools and information needed to deliver an excellent customer experience,” he said.
The company’s data is housed at CCI Global Technologies, Rivian’s data aggregation partner, along with ITAS, the management tool used by network members.
“It allows shop owners to manage all of the things required for the program in a very interactive way,” Phillips explained.
Since joining the company in 2020, Phillips has visited more than 1,000 body shops, evaluating locations to qualify them for certification. Rivian is actively seeking additional facilities to take part in the program.
“To become certified, centers must meet specific requirements such as being up to date on training, having the specialty tools necessary to perform repairs and being conveniently located,” he explained.
Phillips said the OEM has high standards for those interested in joining.
“If you're a well-equipped shop and you're currently working on modern vehicles, you're going to have the majority of the things required to be on the program,” noted Phillips.
A key element of the program is based on relationships. These include the relationships Rivian has with its certified network and facilities have with customers.
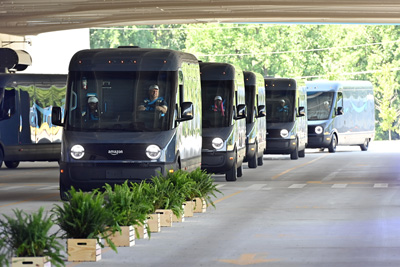
“It’s about ascertaining that are you committed to working with a customer who is in a bad situation and you’re going to deliver the same type of experience Rivian provides its customers,” explained Phillips. “I've got to know without a shadow of a doubt that you're going to stand beside me shoulder to shoulder as we venture into this new car business.”
Those interested in being part of the network must go through a credit check and sign a participation agreement.
After getting set up with the required tooling and equipment, collision repairers are provided training. Once the equipment is onsite and training is complete, a facility goes through a final validation before working on Rivian EVs.
Shops can also expect post-certification actions where team members conduct a quality assessment to ensure the proper equipment is used and OEM procedures are followed.
“It's really focused on the customer and repair quality is how we deliver the best outcomes,” said Phillips.
Rivian manufactures its batteries and drive units in-house, as well as many of the components. Currently, only certified collision centers have access to Rivian parts. In the future, the auto manufacturer expects to offer unrestricted parts to non-certified collision centers for structural components, such as fenders and bumpers.
However, with the car’s sensors and cameras, Phillips said almost every repair on a Rivian EV will require calibration. As a result, facilities must have access to a diagnostic capability. This can be an in-house operation or as of 2023, a partnership with a Rivian Certified Diagnostic Center (RCDC), a new certification added to the certified network to better support this repair requirement.
“We want to ensure the vehicles are fixed safely and properly, but also deliver that customer experience that we all expect,” he said.
Stacey Phillips Ronak