With a passion for creating new products, Erin Suchara joined 3M as a research and development intern in 2019. After graduating from the University of Michigan the following year with a bachelor's degree in chemical engineering, she took on a full-time role at the company as an advanced application engineer in Maplewood, MN.
In addition to representing the modern body technician’s voice, Suchara supports 3M’s worldwide portfolio of body repair materials, primarily adhesives and sealants. This includes performing product testing, engaging with OEMs and connecting with customers to learn what is needed to keep pace with advancements in vehicle design.
“I'm from the Gen Z generation… We like to know what we're doing and why it has a purpose,” explained Suchara. “My job is exactly that. I know what I'm making, who is using it and the difference it's making.”
Hoping to encourage other Gen Zs to join the collision industry, Suchara participated in a panel discussion in April at IBIS USA focused on overcoming the talent shortage. The panel was moderated by IBIS Worldwide CEO Jason Moseley and included Jason Bartanen, Collision Hub’s director of industry relations, and Max Sorensen, senior vice president of operations for Caliber Collision.
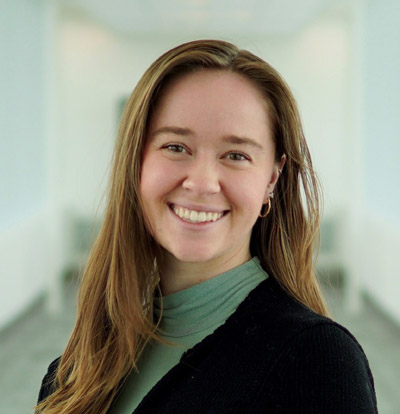
Panelists provided the following insight on providing direction, showing vulnerability and re-messaging the job.
Provide Direction
Sorensen oversees approximately 375 collision centers in the Midwest and Northeastern regions of the U.S., and is dedicated to educating young people about the collision repair industry and helping them reach their potential. He estimates the industry will require around 110,000 technicians over the next five years.
“With the average age of technicians being 47 years old and older, we're going to be aging out technicians,” he noted. “Without bringing [additional] technicians into the industry, we're going to be in a bad place very quickly, especially with the technologies coming.”
In response, Sorensen has played a key role in structuring Caliber’s Technician Apprentice Program (TAP), created for aspiring auto body technicians to acquire the skills necessary to begin a career in the industry. Sorensen also encourages others to get passionate about taking steps to solve this challenge.
“We all need to have a driving force,” he said. “If we don't have that force as an industry, in five years from now, we will be in a bad spot.”
Last year, TAP’s team set a goal to have one apprentice per center.
“We've succeeded in doing that and are past that now,” said Sorensen. “Each of these apprentices is graduating and turning into technicians, and there's a story behind each of those human beings… that's really special.”
He stressed the importance of providing new entrants structure, so they can continue their journey to become technicians.
Suchara agreed. Joining 3M during the pandemic, she said it was difficult to connect and learn with people in the lab. She soon realized the importance of creating structure to be successful.
“My job changes on a daily basis,” she said. “I talk to everyone from product developers to marketers, so having structure for what I do has helped me at the start of my career.”
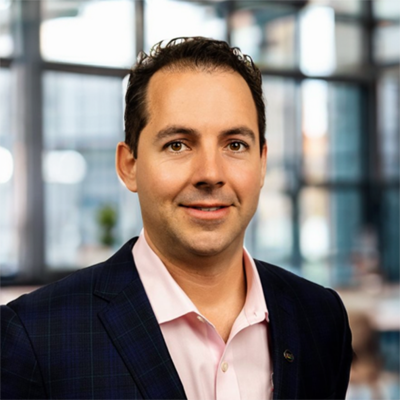
Although smaller shops usually have different challenges than larger ones, Bartanen recommends having employees specialize and learn to excel in certain areas.
“By doing that, I think we'll have safer and more efficient repairs,” he said.
Create a Culture & Career Path
According to panelists, creating a culture and career path is critical to a business’s success.
“Make sure that you have the culture set and there's an expectation of it down the line,” said Bartanen, who leads Collision Hub’s in-shop virtual training and coaching program.
Bartanen suggested becoming part of a local collision repair program to help influence the curriculum for producing skilled technicians and getting involved in the community to raise awareness about the industry. He also encouraged participation in programs such as SkillsUSA.
“It’s one of my favorite activities and has been so rewarding,” he said. “I've seen so many incredible stories of young adults getting involved with SkillsUSA and building a career.”
He has been a member of the SkillsUSA National Collision Repair Technology committee since 1998, where he now serves as committee technical chair.
In addition to young people coming out of school and entering the industry, Sorensen has found adults are also interested in a collision repair career. As a result, he said shops need to work toward providing a career path to help them reach their potential.
Solving the Tech Shortage: Providing Direction, Showing Vulnerability & Re-messaging the Collision Repair Job (article continued)
“We need to be there to guide them through that,” he said. “I'm up here on stage because somebody at my company wanted me to reach my full potential.”
Show Vulnerability
Since she didn’t grow up in a body shop environment, Suchara has learned everything from scratch. Being able to ask questions and learn from mentors has helped her advance in her career.
As a younger employee, Suchara has tried to be more vulnerable.
“Sometimes, I play the new card and say, ‘I don't know,’ and ask questions,” she shared. “It's not always easy to do and doesn't always come naturally.”
However, she typically finds she is the most heard and respected when taking this approach.
When a leader shows vulnerability, Suchara said it helps them connect.
“I couldn't agree more with that, whether you call it vulnerability or humility,” said Bartanen. “That's not inherently what we have done in the collision industry.”
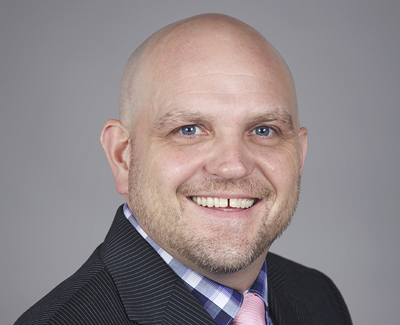
Rather than saying they know everything, Bartanen encourages employees to have the humility to admit they don’t always know, put trust in their research and leverage the expertise of other staff and peers for assistance.
“I think a lot of self reflection needs to happen,” he recommended. “Taking the humble route is a great way to go.”
Be a Disciple
After talking about talent shortage solutions, many find it is challenging to implement new ideas.
Suchara said it’s often more natural to reflect on these issues while attending conferences like IBIS USA. “This event today is kind of a sounding board where I look across the room and see people nodding or hear people reacting to certain things,” she said. “I think it’s easier when you're surrounded by people to take time to reflect.”
“Part of it is that we get back to our normal life---the day-to-day operations---and we have so many different things going on,” added Bartanen. “We need to plan better, think about these things, embrace them and feel like we are going to make a change.”
This includes listening to staff, being empathetic and having a sense of purpose.
To attract new employees, Bartanen advised “…we need to improve our behavior and the way we act and treat people in the shop and the industry. We need to improve that human element.”
He pointed out the industry might not be attractive to many based on comments industry professionals make on social media and some of the regular exchanges that take place in shops. “We need to be better behaved if we’re going to attract and retain talent,” he recommended.
Retention Strategies
One of the outcomes of Sorensen implementing Caliber’s apprentice program was the mentor technician turnover was cut by more than half.
“We turned technicians into mentors,” he said. “Not only did it help with retention, but it was a delightful, unexpected outcome.”
Encouraging technicians to get engaged and active in the industry---whether it’s attending IBIS USA, the Collision Industry Conference (CIC) or the SEMA Show---can also be effective, according to Bartanen.
“Getting them involved and showing you care can go a long way,” he said. “I think a lot of people in the room that have that come into the industry and have stuck with it have had success with good leaders and people who listen and empathize with them.”
Re-messaging the Job
When Suchara entered the industry, she was surprised her role wasn’t advertised as a job that required a lot of skill and had the potential to earn a good wage. “I think the messaging could use a little refresh,” she acknowledged.
“We definitely have to change the narrative because it's not just working with your hands anymore,” said Sorensen. “Technicians need to know the ins and outs of that vehicle because it’s a supercomputer on wheels.”
“Who better to do that than the digital natives… who were born with a tablet in their hands,” added Bartanen.
When people share information about a collision repair career, Bartanen often hears them start by saying not everybody will be a doctor or a lawyer.
“That immediately sets the tone that technical education is a secondary option,” he said. “Why can't we go after the valedictorians? Many of them surely like to work with their hands, are creative and like technology.”
He encourages the industry to look at everybody as a potential job candidate. “Let's not just isolate it based on our preconceived beliefs of what happened when we were younger, when kids were shuffled to ‘that end of the school’ because they weren't the best at math or English,” he said. “You need all those skills now.”
Stacey Phillips Ronak